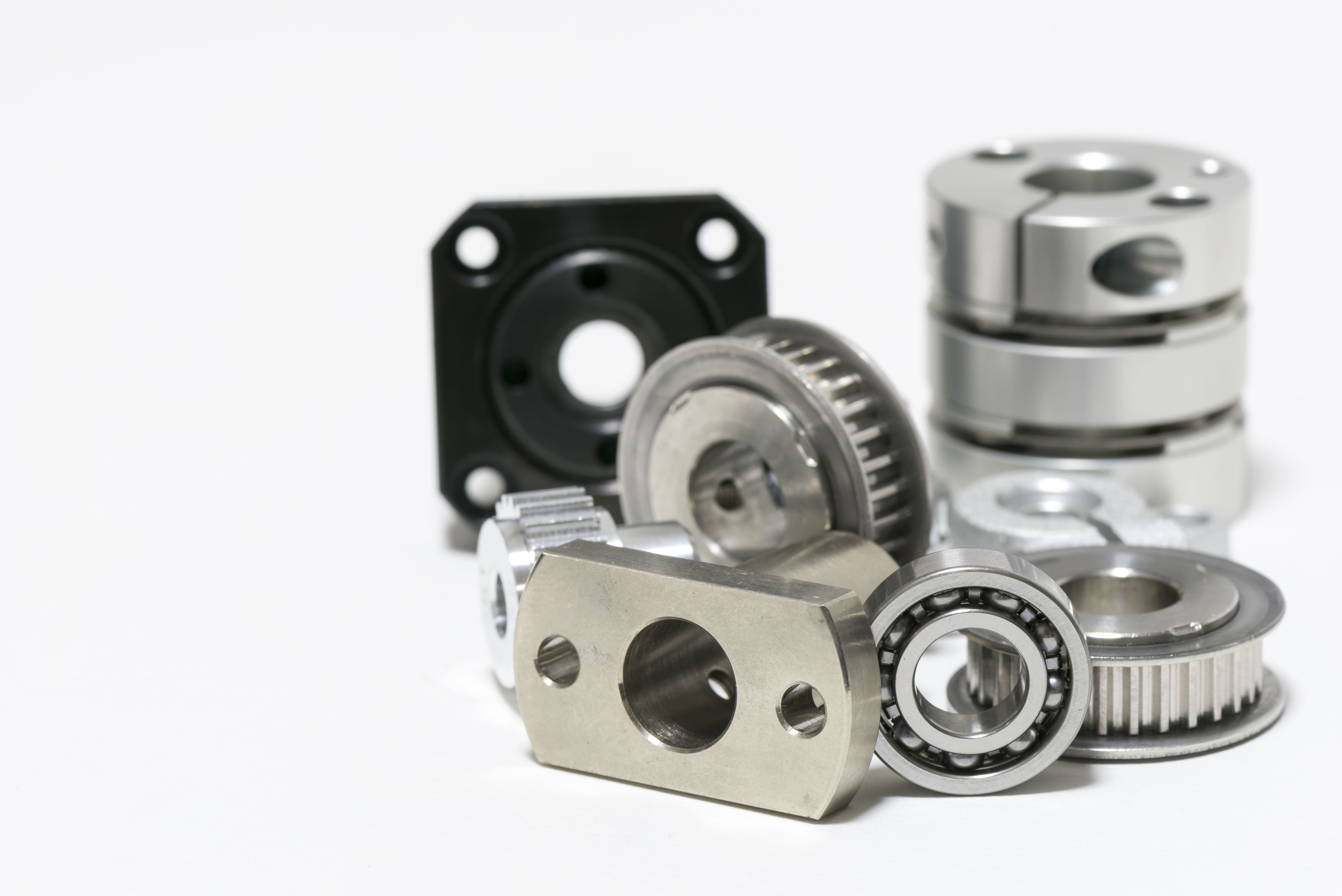
In the realm of crafting top-tier components, achieving an impeccable finish is paramount. The surface quality plays a pivotal role in subsequent processes such as coating, adhesion, plating, or enhancing the final appearance. An effective approach to attaining a superior finish involves the critical cleaning of parts through the process of vapour metal degreasing.
In the pursuit of critical cleaning for components, Midland Deburr & Finish feel a durable and adaptable long-term solution is essential. Even minute traces of surface contaminants, be it oil, grease, adhesives, fingerprints, or other particles, can compromise the efficacy of the finishing process, leading to parts that do not function reliably.
The landscape of critical cleaning has become increasingly challenging, driven by the widespread use of miniaturised parts and intricate geometries. The tighter tolerances of smaller components introduce heightened complexities in manufacturing and finishing. To ensure the optimal performance of intricate components, precision cleaning becomes imperative. However, navigating this process becomes intricate when factoring in challenges such as hard-to-remove residues, cost considerations, and the dynamic environmental and workplace safety regulations imposed on companies today.
Understanding How Vapour Metal Degreasing Works
Vapour metal degreasing is emerging as a comprehensive and effective cleaning process, reclaiming its status in the industry. This method operates through vapour degreasers, which constitute a closed-loop system requiring two essential components: a specially designed cleaning machine and a specific low-boiling, non-flammable fluid as the cleaning agent. The vapour degreaser comprises two chambers: the boil sump and the rinse sump. In the boil sump, the solvent is heated, and the components are immersed and cleaned within the fluid. Subsequently, the cleaned parts are mechanically transferred to the rinse sump for a final rinse in a pure, uncontaminated fluid. The outcome is clean, dry, spot-free components, immediately ready for the subsequent steps in the manufacturing process or for packaging. Using Midland Deburr & Finish for your vapour degreasing means your customer receives parts in perfect condition to then send to their customers.
The cleaning fluids employed in this system possess multiple chemical properties advantageous to critical cleaning. Notably, these fluids exhibit low surface tension and very low viscosity, facilitating easy penetration and cleaning of tight spaces such as blind holes and crevices between stacked parts. Additionally, most vapour degreasing fluids are dense, typically 20-40% heavier than water, aiding in dislodging particulate matter from the components.
In the pursuit of achieving a superior surface quality for finishing, the critical step of cleanliness cannot be overlooked. Thorough investigation is imperative to ensure that components are impeccably prepared for the subsequent stages of manufacture. Midland Deburr & Finish in Lye emerges as your optimal choice for vapour degreasing, solvent degreasing, and metal degreasing needs, offering unparalleled advantages.
Midland Deburr & Finish excels in providing a solution that goes beyond the immediate benefits. The process exhibits remarkable flexibility, seamlessly adapting to any future changes. Whether it involves compliance with evolving regulations, addressing environmental considerations, or accommodating alterations in cleaning requirements, vapour degreasing from Midland Deburr & Finish proves to be a highly versatile and indispensable cleaning process in the realm of finishing. Choosing Midland Deburr & Finish ensures that your components receive the utmost care and preparation, setting the foundation for top-tier manufacturing outcomes.